Efficiency and accuracy are essential in manufacturing to maintain competitiveness and satisfy high-quality standards. Traditional methods are often inadequate when production needs increase, particularly for complex jobs and high-speed manufacturing. Advanced laser processing has become a potent option with its ability to provide precise cutting, welding, engraving, and branding across various sectors.
Businesses’ approaches to production are changing due to technology’s capacity to improve accuracy and optimize operations. In this article, we will examine how advanced laser processing solutions help enhance precision and efficiency.
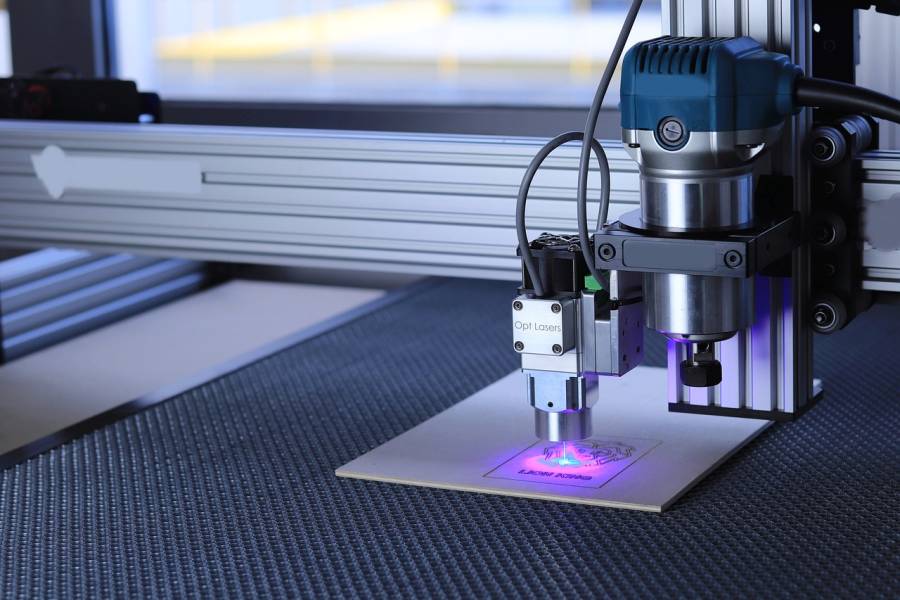
An Overview of Laser Processing Technology
Laser processing modifies materials by cutting, engraving, branding, or welding them using intense laser beams. Thanks to the laser’s tremendous heat, metals, polymers, ceramics, and even biological materials can be precisely manipulated.
This technology enables high-precision material handling, which enables the creation of complex designs and micro-level adjustments. Since each type of laser has special qualities that make it appropriate for particular applications, manufacturers may select the one that suits their requirements.
The laser processing technology offers numerous benefits, such as:
- More accuracy because of laser beams that can be focused down to the thousandth of a millimeter
- Easy automation as it can be easily added to any production line for unprecedented standardization
- Flexible use cases that can be applied across a wide range of materials, ranging from fabric and plastic to glass and metal
- Reduces carbon footprint by minimizing wastage and improving energy efficiency
Therefore, Novanta Photonics says that more manufacturers, especially machine builders, are turning to laser-based technology. The technology is helping them answer complex challenges like controlling micro area design and large-field processing jobs. High-performing laser beam delivery systems combined with precise laser sources produce outcomes tailored to the particular difficulties faced by each machine maker.
Which laser type is ideal for a given material depends on what factors?
The type of laser you should choose depends on the material’s thickness, hardness, thermal conductivity, and needed cutting speed. Fiber lasers are favored for metals, but CO₂ lasers are best suited for organic materials and polymers.
Precision Redefined with Laser Processing
Traditional cutting or engraving equipment might introduce inaccuracy when working with intricate patterns or fragile materials. However, laser technology enables reliable, extremely precise adjustments, which makes it perfect for sectors like electronics, aircraft, and medical device manufacture.
For instance, the U.S. Food & Drug Administration (FDA) strictly regulates the manufacturing process of medical devices. The FDA also recalls products if it finds design flaws that can lead to severe troubles. In 2024, the FDA recalled many flawed IPV therapy devices for the very same reason.
This shows that precision is very important in medical device manufacturing; otherwise, it may lead to recalls or severe legal and financial troubles. Techniques like machining, micromachining, and laser processing are in high demand in this industry. Their popularity keeps increasing because they manufacture sub-assemblies and high-precision, small-profile parts with exceptionally tight tolerances.
What part does software play in laser processing precision?
Software is essential because it enables operators to precisely program the laser’s motions, speed, and intensity. Slight material abnormalities can also be compensated for by sophisticated algorithms, ensuring uniformity in each pass. If software is not used and humans move the laser beams manually, there are high chances of increased wastage and reduced production.
Speed and Efficiency in Production
Besides accuracy, laser processing solutions are also known for their speed and efficiency. This has been seen primarily in 2D materials that require modernization and manipulation.
A Wiley Online Library study states that ultrafast laser processing has become a flexible method for adding new features and altering materials. This technique has shown impressive benefits in manipulating 2D layered materials during the last decade. It has found applications in processes like local patterning, synthesis, structuring, and functionalization.
In contrast to long-pulsed and continuous-wave optical techniques, ultrafast lasers provide a solution for thermal heating problems. Nonlinear interactions between ultrafast laser pulses and the atomic lattice significantly influence the chemical and physical characteristics of 2D materials.
High-speed laser cutting devices can decrease production time, producing huge quantities without compromising quality. Laser processing offers a dependable way to satisfy needs without sacrificing accuracy in sectors like electronics and automotive, where production speed directly influences profitability.
Lowering Costs with Laser Processing
Despite the potentially hefty initial setup expenses, the long-term cost benefits of laser processing are substantial. High repeatability, less material loss, and fewer tool changes are all benefits of laser processing that save operating costs.
Furthermore, compared to traditional tools, laser processing systems often have longer operating lifespans and require less maintenance. This makes them a wise investment for production environments with high demand. Laser processing frees up resources for more innovation and expansion by reducing labor, waste, and maintenance costs.
A team from Korea and Germany is conducting international joint research to enhance the production efficiency of fuel cells through laser machining. Their recently developed technology reduces cross-coupling errors and improves machining quality through more accurate position correction by the scanner’s vision system. The cutting gas nozzle can also be connected independently to the scanner or another stage to enhance cutting quality.

HedgeThink.com is the fund industry’s leading news, research and analysis source for individual and institutional accredited investors and professionals